The support plates
From the beginning
From the end of the 1920s and then in the 1930s, plastics have been the protagonists of countless researches and in-depth studies such as to allow them to be increasingly used in any sector of application, not only at home, but mainly at industrial level. In fact, these are materials with excellent chemical and mechanical properties, equal if not superior to the characteristics of other materials used for centuries, but which have the advantage of easily reducing costs and being durable.
But what do we all commonly call plastics, how do they define themselves from a chemical and physical point of view? These are materials that contain one or more high molecular weight polymers as fundamental constituents, that is, substances consisting of large molecules, called macromolecules, formed by joining according to stable chemical bonds, units called monomers or basic polymers. They are obtained from the oil refining process, which originates heavy naphtha, which processed by catalytic or thermal cracking, produce basic polymers such as elitene, propylene, methane, ethylbenzol, and others. Through subsequent processes and chemical processes (polymerization), the finished products are marketed.
Based on the molecular structure, the material exhibits particular chemical and mechanical properties. The main categories into which they are divided are three:
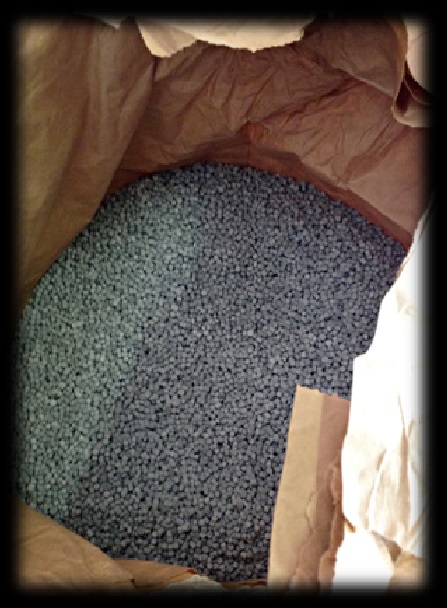
Globally, all these products retain beneficial common properties:
lightness / chemical inertia / low coefficient of friction / low conductivity, both thermal and electrical / good optical properties / relatively low cost, thanks to the inexpensive training processes, the elimination of finishing processes and protective coatings, and the possibility of recycling .
Focus On
By considerably limiting the area of use, specifically in our sector, the polymers most used are POLYETHYLENE and POLYPROPYLENE.
POLYETHYLENE is certainly the most widespread material and constitutes 40% of the world production of plastic materials. Through two different processes, low density polyethylene is obtained, used for the production of packaging, films, containers and as an electrical insulator; and high density polyethylene which, thanks to chemical inertia, can constitute tanks, vessels and pipes.
It is more interesting for us to treat another very important thermoplastic polymer, POLYPROPYLENE, a central element in the production of thicknesses and spacers.
Obtained by polyaddition from propylene gas, it can be homopolymer, block copolymer or random.
At a structural chemical level, a further diversification can be identified: if the substituent groups, in this case the methyl groups, are all located on the same side of the polymer chain, there is a positional isomerism which causes an isotactic structure; otherwise if they are positioned randomly on both sides of the chain, the structure is atactic.
From a commercial point of view the most used is isotactic polypropylene: in fact, having a high crystallinity, the material is rather rigid.
This determines extremely advantageous mechanical properties, a high breaking load, a relatively low density, a reduced percentage of water absorption, a melting temperature of 165 ° C, good insulating properties having a thermal conductivity k of about 0.1-0.22 W / (m K).
The production system
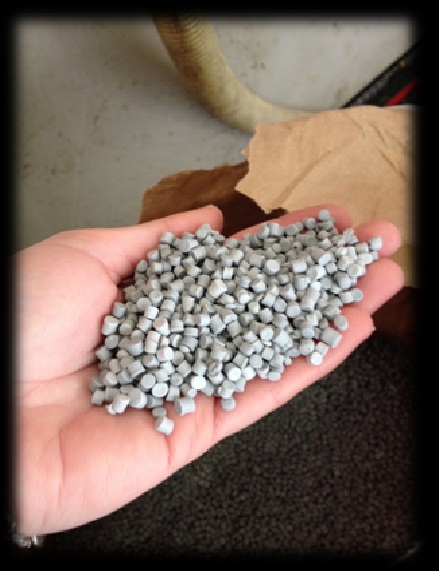
The support systems, that is the plates used in various sectors of civil and construction engineering, are produced by means of a particular forming technology: INJECTION MOLDING.
The granule material is loaded through the hopper into the injection press, or in the feeding area of the rotating screw, positioned inside a cylindrical duct in which resistances are positioned at regular intervals. By rotating the screw, an increase in temperature occurs which brings the material to the fluid state, after which the plasticized material is pushed into the accumulation chamber. Subsequently, the punching screw moves towards the nozzle, pushing the material into the mold.
In this compaction phase, the system must be kept under pressure, so an additional quantity of material is injected to fill the mold entirely, thereby compensating for the change in volume and the possible shrinkage of the material.
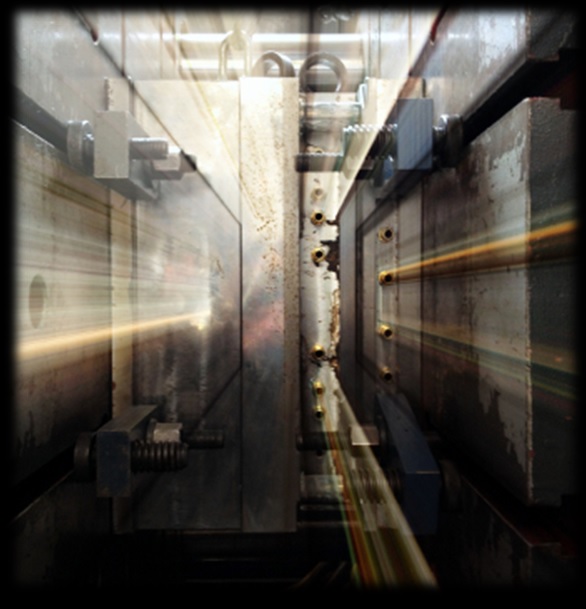
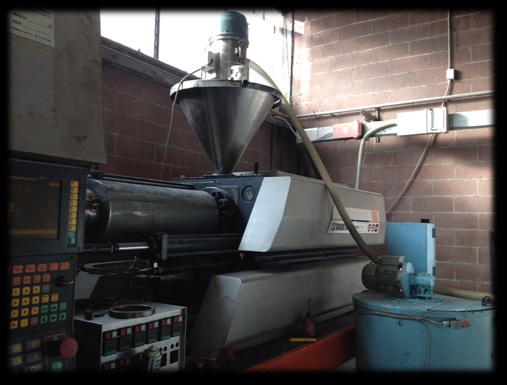
The material therefore remains in the mold for the time necessary for the perfect solidification of the material, catalyzed by controlled cooling by means of jets of cold water. The final product ejection phase is therefore started: the mold opens and the injectors on the moving plate push the article out of the mold.
Since this process allows the molding to two or more figures, more articles are obtained with a single cycle, which at the moment of the opening of the mold are joined by the sprue, which is nothing more than the solidified material in the injection channels.
Once the waste has been removed, the individual items are ready to be marketed.
The thicknesses represent a fundamental entity in the assembly phase of the prefabricated structural components, such as infill panels, beams, pillars. contact over a sufficiently large area.
The support plates
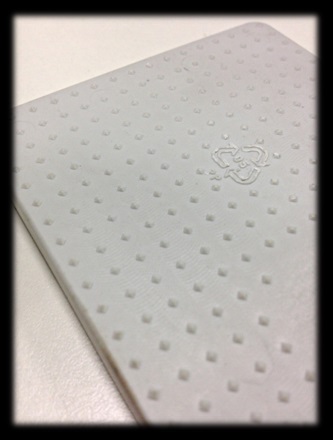
Eye to detail
In a market that offers extensive competition, we wanted to distinguish ourselves by investing in quality and guarantee. Anyone holding a plate of our production in their hands cannot fail to feel the precision that distinguishes it.
The structure is perfectly regular, without bending or unevenness. Both the lower and upper surfaces are enriched by the presence of equidistant pyramidal anchor points, which ensure the correct settling of the superimposed loads and prevent incorrect surface sliding.
Furthermore, aware of the need to be able to count on a valid and exhaustive supply, we have subjected the products to laboratory tests at the relevant bodies obtaining an important certification attesting the resistance without breaking to a compression from 40T up to 100T.
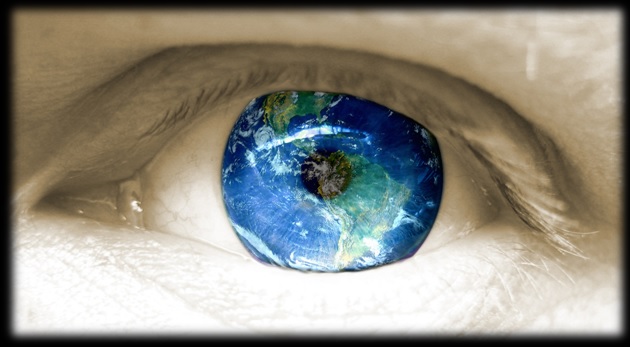